What is blade construction? Blade construction encompasses the design, materials, and techniques used to craft blades for various applications, including weaponry, tools, and machinery.
The choice of materials, such as steel, titanium, or ceramics, significantly impacts a blade's properties, including its strength, durability, flexibility, and resistance to wear and corrosion. The design of the blade's geometry, including its shape, cross-section, and edge profile, determines its cutting efficiency, handling characteristics, and overall performance.
Blade construction methods have evolved throughout history, from traditional forging techniques to advanced manufacturing processes. Modern techniques like laser cutting, CNC machining, and heat treatment allow for precise control over blade dimensions, tolerances, and surface finishes. These advancements have enabled the production of blades with exceptional sharpness, durability, and reliability.
The construction of a blade is crucial as it influences its functionality, safety, and longevity. Proper blade design and construction are essential for ensuring optimal performance, minimizing accidents, and extending the blade's lifespan.
Blade Construction
Blade construction encompasses several key aspects that determine the functionality, durability, and performance of a blade. These aspects include:
- Materials: Steel, titanium, ceramics, and other materials impact strength, flexibility, and corrosion resistance.
- Geometry: Shape, cross-section, and edge profile influence cutting efficiency and handling.
- Heat Treatment: Processes like tempering and annealing enhance blade properties like hardness and toughness.
- Manufacturing: Techniques like forging, CNC machining, and laser cutting ensure precision and consistency.
- Design: Blade construction considers intended use, ergonomics, and safety features.
These aspects are interconnected and influence the overall quality and performance of a blade. For instance, the choice of material affects the blade's strength and durability, while heat treatment can enhance its wear resistance and toughness. The geometry of the blade determines its cutting efficiency and handling characteristics, while the manufacturing process ensures precision and consistency in blade dimensions and surface finishes. By considering all these aspects, blade construction aims to create blades that are sharp, durable, reliable, and safe for their intended applications.
Materials
The choice of materials is a critical aspect of blade construction as it directly influences the blade's performance and durability. Different materials possess unique properties that make them suitable for specific applications.
Steel is a commonly used material for blades due to its strength, hardness, and toughness. It can withstand high impact forces and maintain its edge sharpness for extended periods. However, steel is susceptible to corrosion, especially in humid environments.
Titanium is another popular material for blades. It is stronger than steel, lightweight, and highly resistant to corrosion. Titanium blades are often used in applications where weight reduction and corrosion resistance are crucial, such as aerospace and medical instruments.
Ceramics, such as zirconia and alumina, are gaining popularity for blade construction. Ceramic blades are extremely hard and wear-resistant, making them ideal for cutting hard materials like glass and ceramics. However, they are also more brittle than steel and titanium, requiring careful handling and use.
The selection of blade material depends on the intended application and the desired properties. By understanding the strengths and limitations of different materials, manufacturers can design blades that meet the specific requirements of each application.
Geometry
The geometry of a blade refers to its shape, cross-section, and edge profile. These factors play a crucial role in determining the blade's cutting efficiency and handling characteristics.
- Blade Shape: The overall shape of the blade, such as a straight edge, curved edge, or serrated edge, influences its cutting action. For example, a straight edge is suitable for precise cuts, while a curved edge excels at slicing and contouring.
- Cross-section: The cross-section of the blade, such as a flat grind, hollow grind, or convex grind, affects its strength, durability, and cutting performance. A flat grind provides a strong and durable blade, while a hollow grind reduces weight and improves cutting efficiency.
- Edge Profile: The edge profile, such as a chisel grind, micro-bevel, or scandi grind, determines the blade's sharpness, edge retention, and cutting style. A chisel grind offers a robust edge, while a micro-bevel enhances sharpness and edge stability.
Understanding the relationship between blade geometry and its performance allows manufacturers to design blades that are optimized for specific cutting tasks. By considering factors such as the material being cut, the desired cut quality, and the user's preferences, manufacturers can create blades that deliver exceptional cutting efficiency and handling.
Heat Treatment
Heat treatment is a crucial aspect of blade construction as it significantly influences the blade's performance and durability. Processes like tempering and annealing involve controlled heating and cooling of the blade to modify its internal structure and enhance its properties.
- Enhanced Hardness: Tempering is a heat treatment process that increases the hardness of the blade. By heating the blade to a specific temperature and then rapidly cooling it, the steel's microstructure transforms, resulting in a harder and more wear-resistant blade.
- Improved Toughness: Annealing is another heat treatment process that improves the toughness of the blade. By heating the blade to a high temperature and then slowly cooling it, the steel's microstructure changes, resulting in a tougher and more flexible blade.
- Stress Relief: Heat treatment can also relieve internal stresses in the blade, which can occur during forging or machining. By heating the blade to a specific temperature and then slowly cooling it, these stresses are reduced, resulting in a more stable and durable blade.
- Tailored Properties: Heat treatment allows manufacturers to tailor the blade's properties to meet specific requirements. By carefully controlling the heating and cooling parameters, manufacturers can achieve the desired combination of hardness, toughness, and wear resistance for the intended application.
Overall, heat treatment is an essential part of blade construction as it enables manufacturers to enhance the blade's performance, durability, and reliability. By understanding the effects of heat treatment on the blade's properties, manufacturers can design and produce blades that meet the demands of various applications.
Manufacturing
Manufacturing techniques play a vital role in blade construction by ensuring precision, consistency, and repeatability. Advanced manufacturing processes have revolutionized blade production, enabling the creation of blades with complex geometries, tight tolerances, and superior quality.
- Forging: Forging involves shaping the blade material by hammering or pressing it under controlled conditions. This process imparts strength and durability to the blade by aligning the grain structure of the material. Forging is commonly used to create blades for knives, swords, and other cutting tools.
- CNC Machining: CNC (Computer Numerical Control) machining utilizes computer-controlled machines to remove material from the blade, resulting in precise dimensions and intricate designs. CNC machining is suitable for producing blades with complex shapes, such as those used in aerospace and medical applications.
- Laser Cutting: Laser cutting employs a focused laser beam to cut the blade material with extreme precision. This process produces clean, burr-free edges and allows for intricate designs and patterns. Laser cutting is often used to create blades for surgical instruments and microelectronics.
- Precision Grinding: Precision grinding involves using abrasive wheels to shape and finish the blade surface. This process ensures a consistent edge profile and a high level of surface finish. Precision grinding is commonly used to sharpen and refine the cutting edges of blades.
These advanced manufacturing techniques have greatly enhanced the capabilities of blade construction. By enabling the production of blades with exceptional precision, consistency, and quality, these techniques have contributed to advancements in various industries, including manufacturing, aerospace, and healthcare.
Design
The design of a blade is crucial as it directly influences its functionality, safety, and ease of use. Blade construction considers various aspects of design to ensure that the blade meets the specific requirements of its intended application.
- Intended Use: The design of a blade is primarily determined by its intended use. Different applications, such as cutting, slicing, or piercing, require blades with specific shapes, sizes, and edge profiles. For instance, a chef's knife is designed for precise cutting, while a survival knife is designed for versatility and durability.
- Ergonomics: Ergonomic considerations play a vital role in blade design, ensuring that the blade is comfortable and efficient to use. Faktoren wie Griffform, Griffmaterial und Gesamtbalance der Klinge wirken sich auf die Ergonomie aus. Ein gut gestalteter Griff reduziert Ermdung und verbessert die Kontrolle ber die Klinge.
- Safety Features: Safety is a paramount concern in blade construction. Design features such as finger guards, non-slip handles, and locking mechanisms help prevent accidents and injuries. Additionally, the choice of materials and manufacturing techniques can contribute to the overall safety of the blade.
By considering intended use, ergonomics, and safety features, blade construction aims to create blades that are functional, comfortable, and safe for their intended applications. These design aspects work together to enhance the user experience and minimize the risk of accidents or injuries.
Blade Construction FAQs
This section addresses frequently asked questions and misconceptions surrounding blade construction, providing clear and informative answers.
Question 1: What are the key factors to consider when choosing materials for blade construction?Material selection depends on the intended use and desired properties of the blade. Factors to consider include strength, flexibility, corrosion resistance, and wear resistance. Common materials used in blade construction include steel, titanium, and ceramics.
Question 2: How does blade geometry impact its cutting performance?Blade geometry encompasses the shape, cross-section, and edge profile of the blade. These factors influence the cutting efficiency, handling characteristics, and overall performance of the blade.
Question 3: What is the role of heat treatment in blade construction?Heat treatment processes, such as tempering and annealing, modify the internal structure of the blade to enhance its properties. Heat treatment can increase hardness, improve toughness, relieve internal stresses, and tailor the blade's properties to specific requirements.
Question 4: What manufacturing techniques are commonly used in blade construction?Advanced manufacturing techniques, including forging, CNC machining, laser cutting, and precision grinding, are employed to ensure precision, consistency, and repeatability in blade construction. These techniques enable the production of blades with complex geometries, tight tolerances, and superior quality.
Question 5: How does blade design consider intended use and safety?Blade design takes into account the intended use of the blade, considering factors such as cutting style, ergonomics, and safety features. Ergonomic design ensures comfort and efficiency, while safety features minimize the risk of accidents and injuries.
These FAQs provide a concise overview of key aspects of blade construction, offering valuable insights into the materials, geometry, manufacturing techniques, and design considerations involved in creating functional and reliable blades.
Blade Construction
Blade construction encompasses a diverse range of materials, geometries, manufacturing techniques, and design considerations, each contributing to the functionality, durability, and safety of blades. From the selection of materials to the intricate details of blade geometry, every aspect of blade construction is meticulously engineered to meet the specific demands of its intended application.
The exploration of blade construction in this article has provided valuable insights into the complexities and advancements in this field. It underscores the importance of understanding the interplay between materials, geometry, manufacturing techniques, and design principles to create blades that are not only sharp and durable but also safe and efficient to use. As technology continues to evolve, we can anticipate further innovations in blade construction, pushing the boundaries of what is possible and shaping the future of cutting-edge industries.
Is David Marks From Florida Still Alive After The Shooting?
5 Essential Susan Felder Books To Illuminate Your Literary Journey
Enjoy KFC Catering: The Perfect Solution For Your Events

HOW IT'S MADE From bottle to blade JEC

Makin' the Blade ROTOR Media
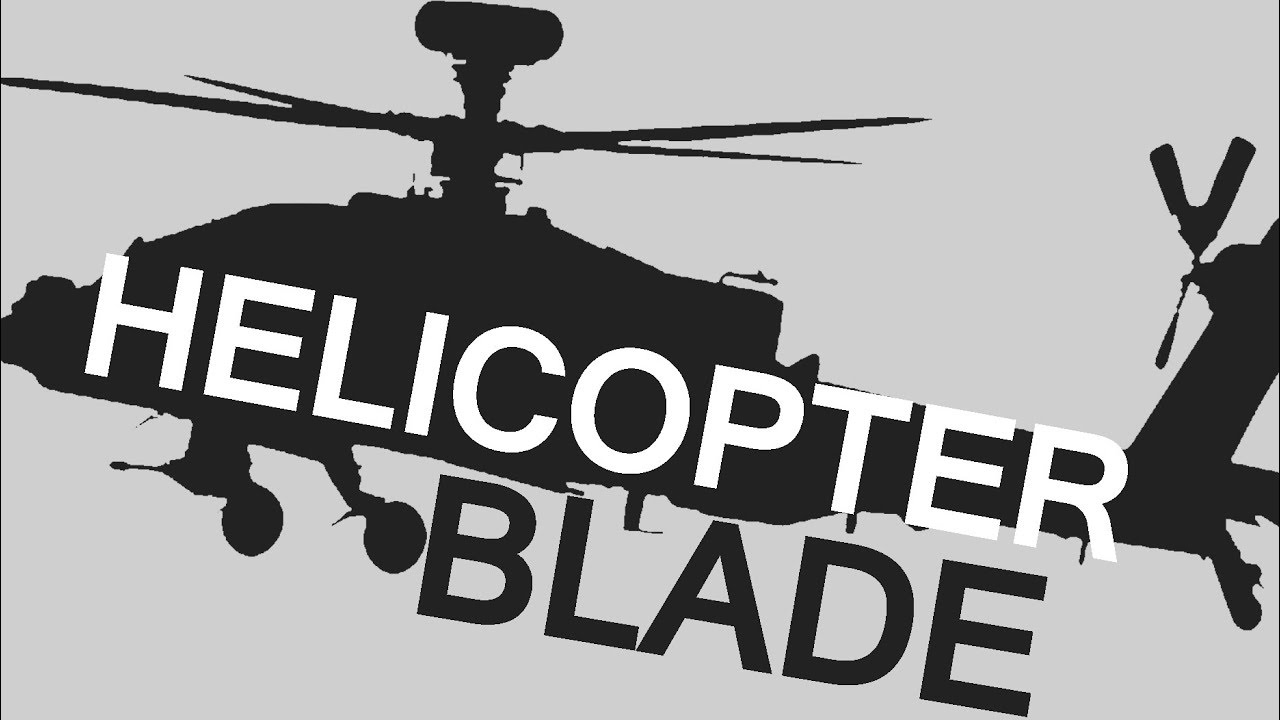
Helicopter Blade Construction YouTube